Hydrogen production by water electrolysis
Hydrogen production by water electrolysis is the dissociation of water molecules under the action of direct current to produce oxygen and hydrogen, which are precipitated from the anode and cathode of the electrolyzer respectively. Depending on the electrolyzer diaphragm material, hydrogen production by water electrolysis is usually divided into alkaline water electrolysis (AE), proton exchange membrane (PEM) water electrolysis and high-temperature solid oxide water electrolysis (SOEC).
Hydrogen production by electrolysis of alkaline water
The diaphragm of the alkaline water electrolysis hydrogen cell consists mainly of asbestos, which acts as a gas separator. And the cathode and anode mainly compose of metal alloys, such as Ni-Mo alloy, which decompose water to produce hydrogen and oxygen.
The electrolyte of industrial alkaline water electrolyzer is usually KOH solution with mass fraction of 20%~30%. Operating temperature of the electrolyzer is 70~80℃, working current density is about 0.25 A/cm2, gas pressure is 0.1~3.0 MPa, overall efficiency is 62%~82%. Alkaline water electrolysis for hydrogen production is a mature technology with low investment. And operation cost, but there are problems such as alkali loss, corrosion and energy consumption.
PEM Hydrogen production by water electrolysis
Unlike alkaline water electrolysis for hydrogen production, PEM water electrolysis for hydrogen production selects for its good chemical stability and proton conductivity. Gas-separating perfluorosulfonic acid proton exchange membrane is used as a solid electrolyte instead of an asbestos membrane, which can effectively block electron transfer and improve electrolyzer safety.
The main components of PEM water electrolyzer are proton exchange membrane, cathode catalytic layer, cathode gas diffusion layer. And cathode terminal plate from inside to outside in order. Among them, the diffusion layer, catalytic layer and proton exchange membrane form the membrane electrode, which is the main site of material transfer. And electrochemical reaction of the whole water electrolyzer. And the characteristics and structure of the membrane electrode directly affect the performance and lifetime of the PEM water electrolyzer.
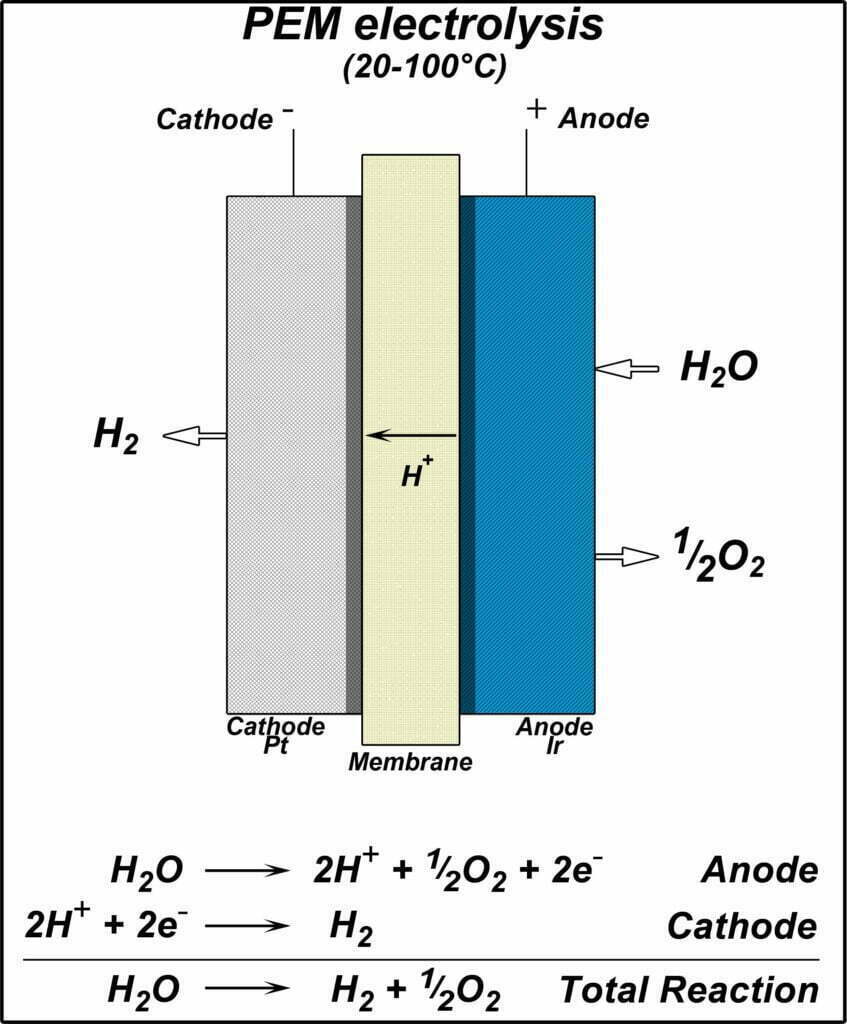
Compared to alkaline water electrolysis for hydrogen production, PEM water electrolysis for hydrogen production has higher operating current density (1 A/cm2). And higher overall efficiency (74%~87%). higher hydrogen volume fraction (>99.99%), higher gas production pressure (3~4 MPa). And faster dynamic response to adapt to the volatility of renewable energy generation. It considers to be a promising technology for hydrogen production by water electrolysis.
At present, PEM water electrolysis hydrogen production technology demonstrat. And gradually promoted in the fields of hydrogen production on site at hydrogen refueling stations. Hydrogen production from wind power and other renewable energy sources by electrolysis, and energy storage.
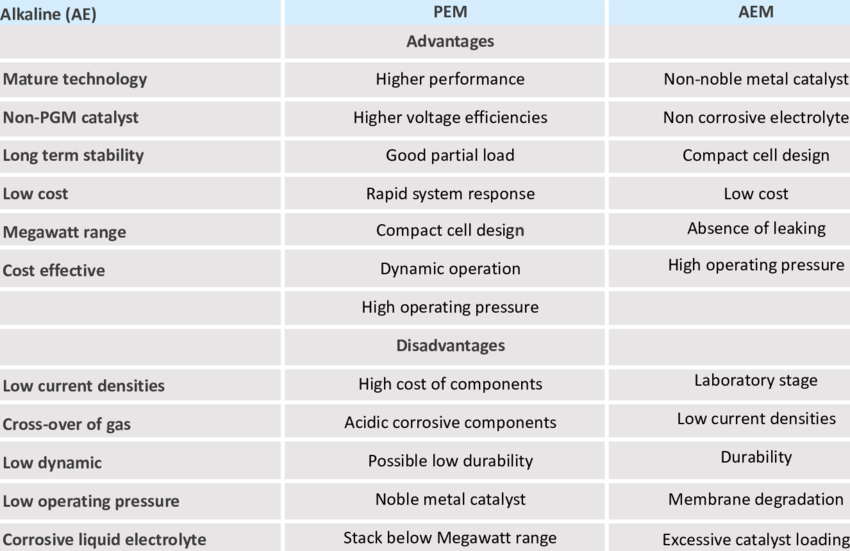
High-temperature solid oxide water electrolysis for hydrogen production
Unlike alkaline water electrolysis and PEM water electrolysis. High-temperature solid oxide water electrolysis for hydrogen production uses solid oxide as the electrolyte material. And the working temperature is 800~1,000℃. Significantly improved electrochemical performance and higher efficiency of hydrogen production process.
SOEC electrolyzer electrode adopts non-precious metal catalyst, cathode material selects porous metal ceramic Ni/YSZ. An anode material selects chalcocite oxide. Electrolyte adopts YSZ oxygen ion conductor, all ceramic material structure avoids material corrosion problem.
The high temperature and high humidity working environment restricts the selection of materials with high stability, good durability. And decay resistance for the electrolyzer. Also, it restricts the selection and large-scale promotion of SOEC hydrogen production technology application scenarios.
